W-Tools AB in Alvesta has many years of experience. The company was founded by Carl-Göran Andersson in 1988, who already had extensive experience with unscrewing moulds. This also became the primary product for the company during the first year. Over the next couple of years, the company expanded and began manufacturing other types of moulds.
Per-Anders Säll Andersson, the current CEO, has been with the company from the beginning, as his father was its founder. He was also part-owner until 2011, when Per-Anders and Carl-Göran sold their company to a private investment firm.
W-Tools clients are manufacturers in the plastics industry, and their end customers are primarily involved in food packaging, medical technology and electronics. Their customers are generally in the local area, in and around Växjö and Lagan.
Moulds are manufactured in classic tool steel, which then undergoes heat treatment to achieve the hardness required. Moulding materials are purchased from a company in Hagfors, which specialises in this type of material. Currently the company is in the process of manufacturing moulds for detergent and hand sanitiser dispensers. There has been a greater need for these due to the Corona pandemic.
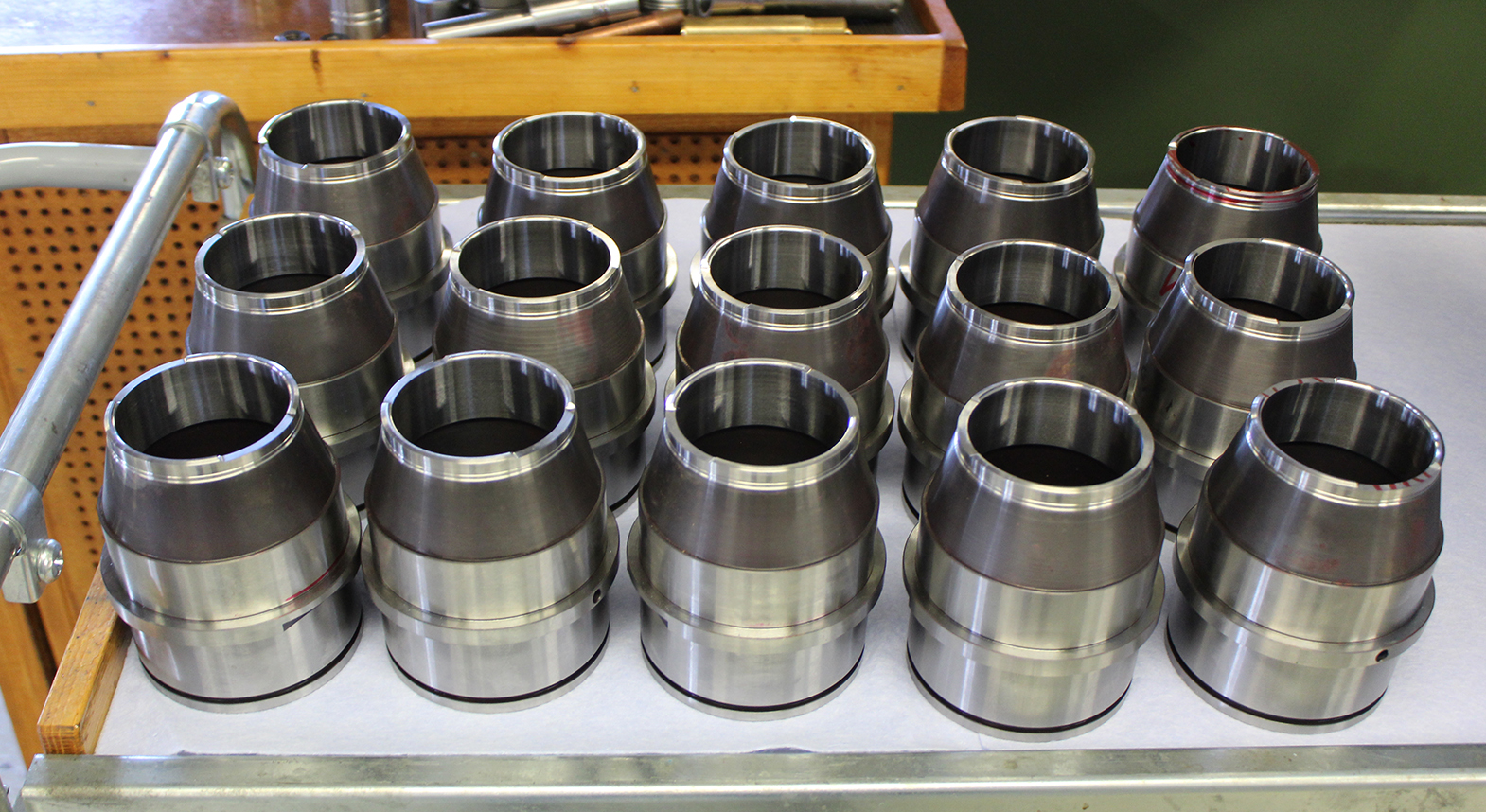
Over the years, they have manufactured moulds for many well-known brands.
– My father was involved in developing the mould for the very first Bliw soap dispensers, says Per-Anders.
W-Tools can provide their customers with expertise all the way from ear to mouth, and has manufactured products that are unique for each client.
– The products may be similar, but are often unique for each assignment, say Per-Anders.
New customers get a 3D model of what their end product will look like, as well as information about the volume of the product to be manufactured by the mould. This is followed by the estimated price and delivery time.
– Take for instance the mould for hand sanitisers now being manufactured. There will be about 24 pieces in each form, every nine seconds.
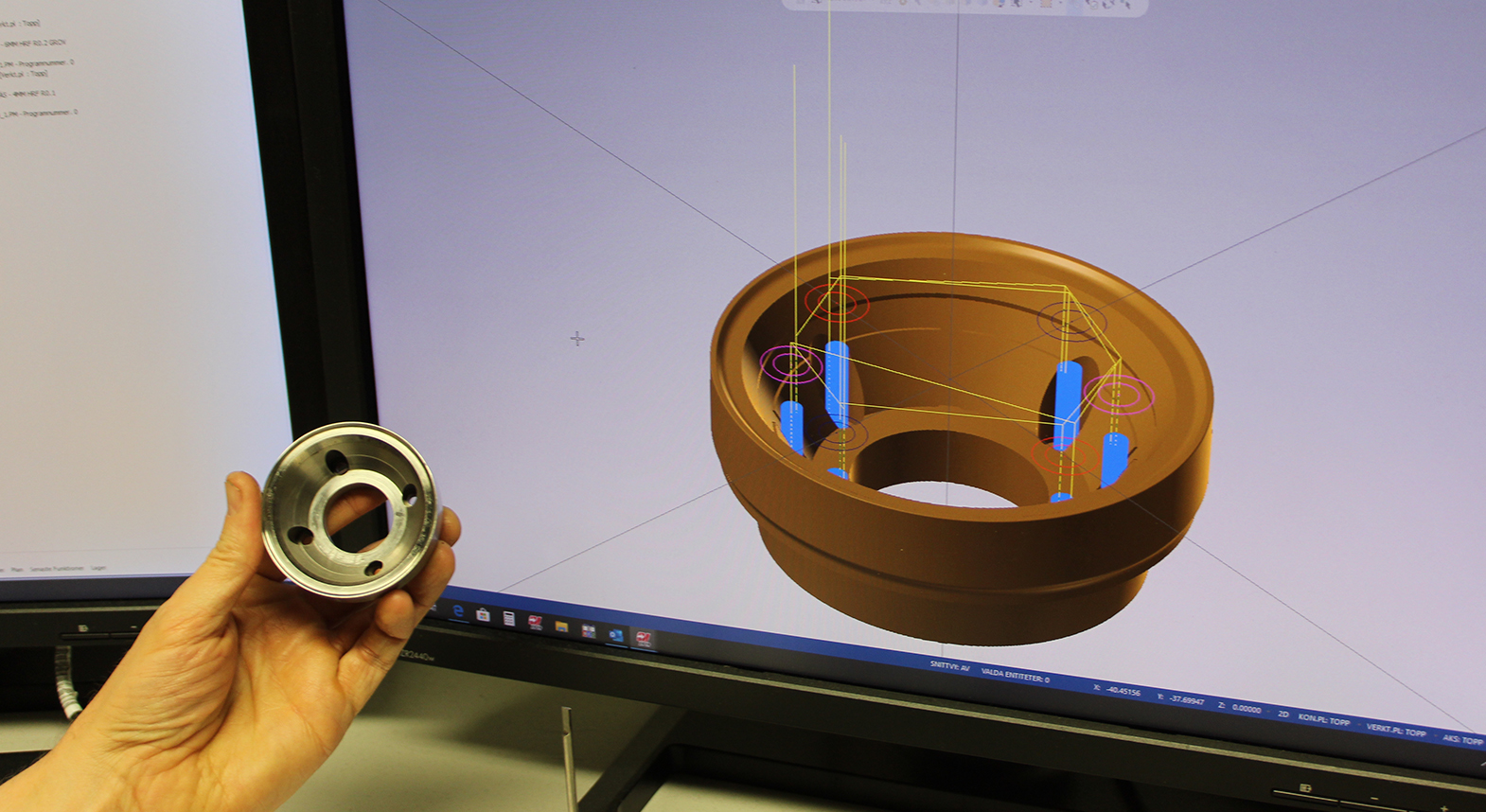
The time it takes from order booking to finished product varies, although for larger projects, the product can usually be delivered within 16 weeks. There are a few different methods for designing a mould, and the company’s extensive experience in unscrewing moulds make them stand out from the rest.
– For deeper threads, it is necessary to rotate the product, and then eject it. This makes them one of a kind. It includes many moving parts, and a lot can go wrong. Therefore, many companies that are not used to doing what we do tend to back out.
The company currently has ten employees, and are looking to hire additional personnel. The most important characteristic of potential employees is an interest in the business and the willingness to learn.
– We can supply the knowledge. I've been working here for thirty years, but I’m still not finished learning. You learn new things all the time. This is why we are looking for additional workers who are willing to learn new things, says Per-Anders.